PRODUCTS QUALITY CONSISTENCY
- Sidney T. Angsanto
- Jun 14, 2017
- 21 min read

CRITICAL SUCCESS FACTOR | KEY RESULTS AREA
To deliver Consistent Quality Products to Customers with Shelf - Life Parameters and Performance Metrics At Competitive Prices With Good Profit Margins
KEY PERFORMANCE INDICATORS
SPECIFIC -MEASURABLE -ACHIEVABLE -RELEVANT -TIME BOUND + MGT CONTROL
INTERCONNECTED, INTER-RELATED and INTEGRATED Application of BALANCE SCORECARD KPI-SMART 4 Perspectives (CUSTOMERS, FINANCE, INTERNAL BUSINESS PROCESSES, ORGANIZATIONAL CAPACITY | LEARNING AND GROWTH) to a Company's "Critical Success Factor (KRA)
ABOUT KPI-SMART
CUSTOMERS
(Distributors, Dealers, Retailers and End Consumers)
To deliver Consistent Quality Products to Customers with Shelf - Life Parameters and Performance Metrics At Competitive Prices With Good Profit Margins
FINANCIAL |
Corporate Planning (a Strategic Management Tool to Map out a Course of Action that will result in Revenue Growth & Increase Profits by making Internal Operations more effective & productive)
1. Budget for the CONSISTENT QUALITY PRODUCTS from Raw Materials to Finish Goods to ensure Customers' Orders are received in Good Condition (down to the End Consumers).
1.a. Warehouse Inventory remaining balance good for one week (from LOCAL Supplier | Production with maximum of 4days to one week lead time) vis-a-vis receiving of delivery | partial transfer. Example - 4 days maximum LT, have ORDERING POINT when items good for 8 working days. With this system, your periodical ending balance will be limited to a maximum of 8 days and not more than that will only be spoiled soon and or cost of money. Moreover, CASH FLOW BALANCE will be Liquid.
1.b. At least 3 Suppliers for each item. Preferably with Terms and Credit Lines.
Benefits:
(a) Quality Products delivered will be consistent (as agreed in Products Specification or Technical Informations like Product Preservation Standard Parameters including Shelf Life | careful in handling | others)
(b) Prices will be competitive. Terms and Credit Limits as well.
(c) Prompt Delivery Services
(d) Good After Sales Services
(e) Others
1.c. Ensure (PPS-QIP) PRODUCT PRESERVATION STANDARD and QUALITY INSPECTION PROGRAM are 100% complied throughout the INVOLVED ORGANIZATION to prevent rejects due to defects, spoilage and cost of money.
1.d. Have weekly Lot (Number of Batches) Production for quality high yield mileage over usage of Man Power, Inventories and Utilities for Cost Efficiency - Preparatory and Post Production Cost to be spread over the Yields.
Average cost per Product SKU will be competitive therefore, more profit.
1.e. Closely work with the Plant Officer for CAPEX with Monthly Schedules for increase in Productivity, Logistics, and Storage if requires
1.f. Develop an Accurate and Real Time (almost due to transmittal process) Information | Performance Metrics to have an effective courses of actions with the following format (sample in brief one)
Use Customized SoftWare or Excel Link eFiles to Auto-Generate the MIS from Raw Data Transaction Encoding
COSTS (Kilos, Quantity, Time, Peso, Percentage) ANALYSIS for CONTROL PARAMETERS [for Quality Consistency and Yields Mileage over Time & Motion, Inventories Usage, Facilities including Utilities] and REAL TIME PERFORMANCE METRICS
Daily Utilities Cut-Off Meter Readings for Costing
[1] Electricity
[2] Water [3] Shellane
[4] Oil [5] Others
(a) PRODUCTION Per Lot and Each Batch (total processes)
For Commissary | Manufacturing (may include Snack Foods, Juices, Plastics, Flexible Packaging [Roto Gravure], Printing Press, others related) | Restaurants
a.1. Per Product
a.2. Per Process (Assembly WIP)
a.3. Others such as Preparatory and Post Operations for each Assembly in a Lot Production (total number of batches minimum). Maybe relevant to restaurants who partially cooks and pack per serving sizes.
(b) Per DEPARTMENT with Section Breakdown
For None Production Related Sections | Departments | Divisions - base on TRANSACTION COUNTS PER HOUR.
(c) LOGISTICS Cost Analysis
c.1. Drop Systems Per Van Route Trip Cost Over Revenues
c.2. Per Outlet delivered Over Revenues
c.3. Others
(d) WAREHOUSE FINISH GOODS (WFG) Cost Analysis of its Operations
d.1. Control Parameters (Time and Motion, Transaction Count), and Performance Metrics
Cut-Off Time in Receiving Orders for following day's deliveries in 3Cs (Communication, Coordination and Cooperation) with Logistics in reference to WFG's preparation base on drop system lay-out (first batch load into the Van for last drop outlet) including Dispatching Time. In order for WFG to schedule the preparation of orders per drop (first to load outlet into the Van), piling per drop - bottom are the Hard | Bulky | Heaviest (sealing), others. As well as Man Power Scheduling, the Facilities (particularly the area for turn-over to Logistics' Van Driver or Helper), Pallets and or Crates per Outlet, Shrink Wrap, and Handling Equipments.
Separated Frozen, Chilled and Dry Items Per Outlet will have to be separated
d.2. NUMBER of TRANSACTIONS (Number of Outlets | Revenues, Cost & Profit | Percentage of Total Cost Per Trip Over Revenues | others ) per Van Trip Costing for LOAD CONTROL PARAMETERS (Upper to Lower Limits) PROTOCOL.
d.3. QUALITY of PRODUCTS PARAMETERS and PERFORMANCE METRICS - Cost Analysis
Performance Metrics (Quantity and Cost of Returns, Rejects, & Other Related Loses) in relation to PPS-QIP (Product Preservation Standards - Quality Inspection Program), as well as FIFO Rotation & Replenishments for Compliance and Continuous Improvements
d.3.a. (PPS) PRODUCT PRESERVATION STANDARD PARAMETERS and its (QIP) QUALITY INSPECTION PROGRAM Compliance Report
(a) Spot Audit before any withdrawals preferably
(b) Or upon withdrawal | issuance though may incur multiple handling cost
(c) Others
Note for Outlet receiving from Logistics Van - in the presence of the Customers (Outlet Officer)
d.3.b. FIFO (FIRST IN - FIRST OUT) LAY-OUTS SET-UP AND POLICY to prevent Spoilage
(a) Economical Floor Lay-Out Process Flow
a.1. From Receiving of Finish Goods (Cut-Off Time to Optimize Yield Mileage over Man power time and motion, etc.) to Queue | Piling Standard and Proper Tag, FIFO Rotation and Replenishments [Items in Queue Piles will only be handled to the Warehouse Rack Shelving (Top Most or Nearest Receiving Door Stocking Area for Last-In, Last-Out)
a.2. SKU FIFO Rack Levels Flow (Bottom for Issuance - oldest stocks though within acceptable Shelf Life Parameters for Factory Plant)
a.3. SKU BIN (Standard shelf allocated column) Pile System - Innermost are supposedly for Last Out
a.4. From Preparation of picking for Issuance, handling, then to proper turn-over floor lay-out
Diagrams, Illustrations in Specific Post or Wall as Guide | Bulletin Board
d.4. INVENTORY MANAGEMENT Cost Analysis
(a) Daily Cut-Off of Ending Inventories Cost (Quantity per SKU) base on Lead Time from Production
(b) Percentage of used storage space from potential revenues
(c) Others
d.5. Other WFG costing that will also include Over Time Pay
(e) WAREHOUSE RAW MATERIALS and SUPPLIES (WRM&S)
e.1. CONTROL PARAMETERS (Time and Motion, Transaction Count), and Performance Metrics
Cut-Off Time in Receiving Production Requests for following day's or shift's deliveries in 3Cs (Communication, Coordination and Cooperation) with Production Sections in reference to WRM&S's preparation base on each of the Production Assembly's (Stage) Preparatory Schedules. In order for WRM&S to schedule the preparation of each ones' request, piling per Assembly Area, others. As well as Man Power Scheduling, the Facilities (particularly the area for turn-over to each Authorized Production Assembly Operator), Pallets and or Crates per Assembly, and Handling Equipments.
Bulk Assorted SKUs Piling Standard per Handling Batch to each Assembly Area.
e.2. TO MINIMIZE LOSS of OPPORTUNITY TO PRODUCE and SELL
e.2.a. Use or develop SCM WRM&S EOQ (Economical Ordering Quantity base on Suppliers' Lead Time) to do its Essential Role and 3Cs (Communication, Coordination and Cooperation) with Purchasing though do 3Cs first with Production.
e.3. NUMBER of TRANSACTIONS Per Hour Costing base on Parameters KPI
e.3.a. Man hour (Time and Motion | Procedures)
e.3.b. Average Cost Per Transaction
e.4. QUALITY of PRODUCTS Parameters and Performance Metrics - Cost Analysis
Performance Metrics (Quantity and Cost of Returns, Rejects, & Other Related Loses) in relation to PPS-QIP, as well as FIFO Rotation & Replenishments for Compliance and Continuous Improvements
e.4.a. (PPS) PRODUCT PRESERVATION STANDARD Parameters and its (QIP) Quality Inspection Program Compliance Report
(a) Spot Audit before any withdrawals preferably
(b) Or upon withdrawal | issuance though may incur multiple handling cost
(c) Others
Note for Outlet receiving from Logistics Van - in the presence of the Customers
e.4.b. FIFO (First In - First Out) Lay-Outs to ensure Quality Consistency of SKUs to prevent loses due to rejects and spoilage
(a) Economical Floor Lay-Out Process Flow
a.1. From Receiving of Finish Goods (Cut-Off Time to Optimize Yield Mileage over Man power time and motion, etc.) to Queue | Piling Standard and Proper Tag, FIFO Rotation and Replenishments [Items in Queue Piles will only be handled to the Warehouse Rack Shelving (Top Most or Nearest Receiving Door Stocking Area for Last-In, Last-Out)
a.2. SKU FIFO Rack Levels Flow (Bottom for Issuance - oldest stocks though within acceptable Shelf Life Parameters for Factory Plant)
a.3. SKU BIN (Standard shelf allocated column) Pile System - Innermost are supposedly for Last Out
a.4. From Preparation of picking for Issuance, handling, then to proper turn-over floor lay-out
Diagrams, Illustrations in Specific Post or Wall as Guide | Bulletin Board
e.5. Inventory Management Cost Analysis
(a) Daily Cut-Off of Ending Inventories Cost (Quantity per SKU) base on Lead Time from its Suppliers.
(b) Percentage of used storage space from the entire storage cost
(c) Others
d.6. Other WRM&S costing that will also include Over Time Pay
(f) Many More in Cost Analysis for Continuous Improvement of Quality, Productivity and Efficiency for Profit and Growth
2. INCREASE SALES AND COLLECTIONS
a. EXISTING CUSTOMERS
b. CREATE NEW MARKETS
INTERNAL BUSINESS PROCESSES (IBP) |
TQM (Total Quality Management) - as an Approach to Management that Embeds Awareness of Quality in All Organizational Processes. Improving process efficiency brings about many benefits in terms of Costs & Time.
PROCESS ROLL-OUT PLAN
* CPA (Critical Path Analysis), PERT (Performance Evaluation and Review Testing), T&M (Time & Motion) - GC (Gantt Chart) | PARAMETERS for Standard Quality Yields Mileage from Usage of Inventories, Man Hour, Utilities and Facilities, including Performance Metrics:
(1) Economical Physical Lay-Outs (U formation Floor Lay-Out including FIFO Rotation and Replenishments, FIFO Racking (Shelving or Pallet Position) Systems, Standard Piling System per SKU, Micro Units' Working Tables, Handling and so on)
1.a) Standard Piling (Pallet, Boxes, Sacks, Etc) System Per SKU for easy counting by the turn-over of Accountability
1.a.i. Number of Quantity Packs per Level & Lay-Out like 3 (vertical) X 2 (horizontal) that will fit into a 5' X 5' Pallet as an example for easy counting with out holding and as well as for stability when piled (height wise)
1.a.ii. Number of Levels (height) that will fit the Rack Shelf Slot though just right so not to fall
1.a.iii. Tag : Item SKU Code | Product Name | Total Quantity | Shelf Life Date | Piled by - name and signature with date and time
1.b. Training Program (Process Roll - Out Plan)
1.b) Standard Rack Shelving (BIN) - Bin Card per SKU
Pallet Position | Shelf Bin
1.c) Standard Racking Flow System per SKU Pile (Pallet or Shelf Bin)
Newly Received at Top Most
Oldest Stocks at Bottom or Ground Level
(2) Each Micro Unit (Assembly) Personnel's Proper Posture, Flow of Movements, Standard Position of Materials (either left to right or the other way around depending in the Macro Process Flow (U-Formation - from Raw to WIP then to Finish)
* Process Flow Charts involving Balance Organizational Structures (Command Accountability Chain and Cross Functional Management cascading down to each Micro Units);
Control Forms Templates (number of Copies) | crucial contents with Signatories (reported by | checked and validated by | Approved by | Received by) with Cut-Off Time,
Attachments of Supporting Documents in proper sequences (may cover photos and videos),
Materials and Inventories,
Equipments and Machines,
IT Systems for accurate and real time MIS from Raw Data Encoding (may use Excel Linked Files),
Training Programs,
Check List, Tally Sheet Turn-Over, Diagrams and Illustrations for Guidelines (Posted to Section Wall or Post), Policies, etc.
1. ORGANIZATIONAL PROCESSES for an Efficient and Efficacious PRODUCTS QUALITY CONSISTENCY Management involving the Command Accountability Chain and Cross Functional Management cascaded down to each Micro Units.
BALANCE ORGANIZATIONAL STRUCTURE with Each Ones' KRAs, Key Functions and KPI-SMART Parameters and Metrics
(a) Quality Assurance Manager (QAM)
[1] Create, develop PPS-QIP Parameters and Performance Metrics including Training Programs particularly the QC Department to ensure Products Quality Consistency from Raw Materials Receiving (suppliers deliveries) to Finish Goods, Logistics to Outlets, then to End Consumers
[2] Ensures QC Compliance through Spot and Regular Audits
[3] Accountability Systems - CCTV, Documentation Trail and so on
(b) Quality Control Manager
[1] 100% compliance to PPS-QIP Parameters and Metrics among his | her command accountability chain.
[2] 3Cs with QAM for continuous improvements
[3] Spot Audit his | her Staffs' Products yields
(c) Factory Plant Sr. Manager - reports directly to the General Manager (GM does the SCM in a SME scale)
[1] Ensures that All his | her Direct Reports are Accountable by spot audit the physical yields per stage, assembly line up to the Logistics for Quality and Smooth Flow of the Operations
(d) Officers from Logistics, Warehouse Finish Goods, Production, Warehouse Raw Materials and Supplies
(e) Purchasing Officer
[1] 3Cs with Warehouse Raw Materials and Supplies In-Charge for # of days supply per sku, quality and shelf life metrics
[2] 3Cs with the Suppliers particularly in the Compliance on Quality Parameters of the Products
[3] 3Cs with the. Production Manager & Plant Sr. Manager of the Raw Materials Shrinkage Value Metrics base on the Parameters in Producing
(f) Officers from National Operations (Stores Chain - Regional, and Areas Officers) - to minimize loses should there be lack of supplies especially in relation to Quality Products Supply
(g) External Customers (Distributors, Dealers, Retailers, End Consumers)
(h) External Suppliers for Products (Trade), Raw Materials and Supplies, Equipments, etc. (may include 3rd party Logistics)
(i) Operations Audit Head - checks and balances of tangibles from documents for variances and accountability control from Raw Materials to WIP then to FG including Quality of the Products with 3Cs with QC and QA
(j) Compliance Audit Head - to ensure 100% compliance on Parameters on site and in reference to Metrics Monitoring for continuous improvements
(k) HRD Head - Training Programs, Pooling, etc.
(l) Admin Manager - for Accountability Systems particularly to prevent or minimize incidents
(m) Finance and Accounting Manager
[1] For budget management, costing and control, etc.
[2] 3Cs with Purchasing and SCM regarding to budget schedules
[3] 3Cs with Others specifically the Plant Resources for Quality Assurance
1.a. QA Develops IN-DEPTH "PPS-QIP" (PRODUCT PRESERVATION STANDARD - QUALITY INSPECTION PROGRAM) System preferably with Auto - Notification with cut-off time via email, text, viber, OneNote for Close Communication, Coordination and Cooperation as to Products Quality Metrics (for Purchasing & Suppliers | Production | Warehouse Raw Materials | Warehouse Finish Goods | Logistics | Operations [Stores Heads] | Sales and may include Marketing | Factory Plant Executive | SCM | GM)
1.a.a. Both External and Internal Customers & Suppliers
1.a.a.1) External Customers (Real Customers who place the orders and pay)
1.a.a.2) External Suppliers (Real Suppliers who delivers and collects)
1.a.a.3) Internal Customers (Departments: Operations, Sales, Marketing, Business Developments, Finish Goods Warehouse, Logistics, Production, Raw Materials and Supplies Warehouse, QC, R&D, QA, Purchasing)
QUALITY STANDARDS and PROCEDURES | POLICIES:
QUALITY AND QUANTITY [Weight / Piece example Fresh Chicken Whole Leg] PARAMETERS [Approved Upper and Lower Control Limits) and PERFORMANCE METRICS
Note:
Set Parameters and Performance Metrics for Control and Continuous Improvements.
Can use Real Time Metrics to determine Compliance in a Section or Department.
Example in a Production Assembly, when Yields Mileage Over Usage of Raw Materials is low than expected, and or sub-standard quality condition - the Assembly Personnel usually did not comply to the Parameters, unless something is wrong with the Raw Materials' Quality and or the Machine Condition.
1. INVENTORIES:
Raw Materials, Work-In-Process, Finish Goods, Van, Outlets
CATEGORIES:
Food, Non-Food
(need to break this down)
SUB-CATEGORIES - FOOD
FROZEN | CHILLED | DRY
SUB OF SUB-CATEGORIES - FOOD | FROZEN
CHICKEN | PORK | BEEF | SEAFOODS
Each SKU ACCEPTABLE CONTROL LIMITS
UPPER | LOWER
(a) PRODUCT PRESERVATION STANDARDS per SKU (Stock Keeping Units)
QUALITY ASSURANCE To Author
Quality Control Department to comply
Columns in Excel Raw Data Master List
a.1. SKU Code (Category | Sub-Category | Item)
a.2. SKU Product Name
a.3. Packaging (Small, Medium, Large, etc.)
a.4. UOM (Unit of Measurement) - Weight (kilos), Quantity Piece (Per Pack B, Per A or Total)
a.5. Technical Specification Parameters
(a) Appearance | Presentation - Photo [Color | Texture | Size] and Brief Descriptions
(b) Shelf Life (depends in the receiver: Division for example: Factory Plant, Distributors, Dealers, Retailers and End Consumers)
(c) Weight
(d) Sense of Sight from open pouch, Smell, Hearing (if applicable) - Brief Descriptions
(e) Touch for Texture | Freshness
(f) Temperature
(g) Others
NOTES:
For Frozen Products: No Moist | Ice Crystals
APPLY CONCEPT TO NON-FOOD PRODUCTS

(b) QUALITY INSPECTION PROGRAM - SET OF ORGANIZATIONAL PROCEDURES & POLICIES
Process Flow Charts, People Involved,
Control Forms with Serial Numbers - # of copies and signatories with cut-off time,
Attachments and Support Documents including Photos / Videos,
Tally Sheets, Check Lists, Diagrams, Illustrations, etc.
IT software and Infrastructure - Tablet may be included if has budget, etc.)
Manual
Training Programs
QUALITY ASSURANCE To Author
Quality Control Department to comply
b.1. FACILITY where QIP will be conducted at Random base on Certain Percentage or 100% - Clean, Sanitized, Hygienic, Temperature | Humidity within Parameters
Not slippery
b.2. REEFER'S
b.2.a. Sealed Doors
b.2.b. Temperature of Van
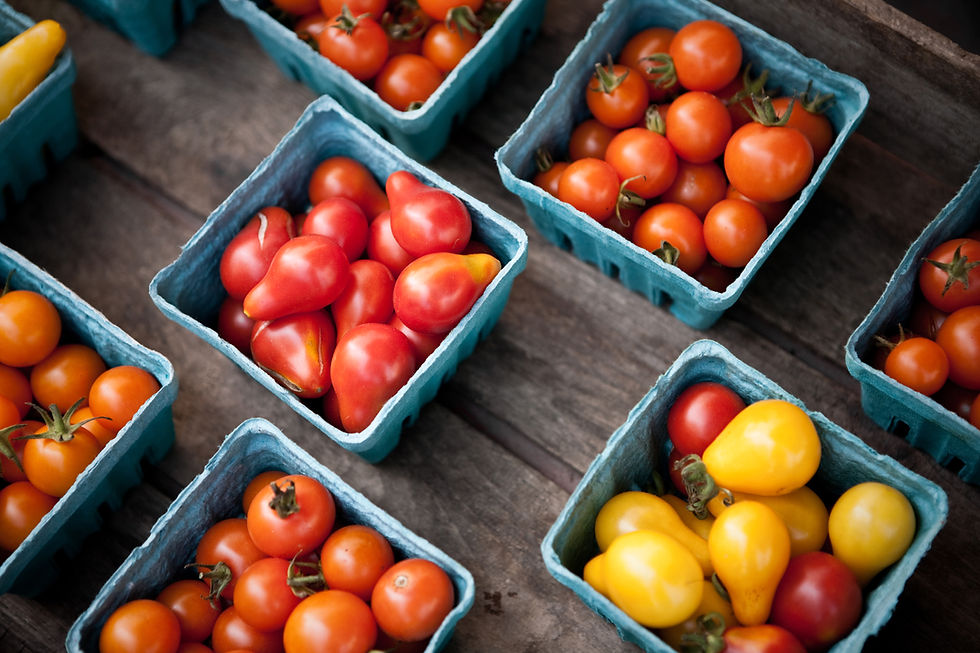

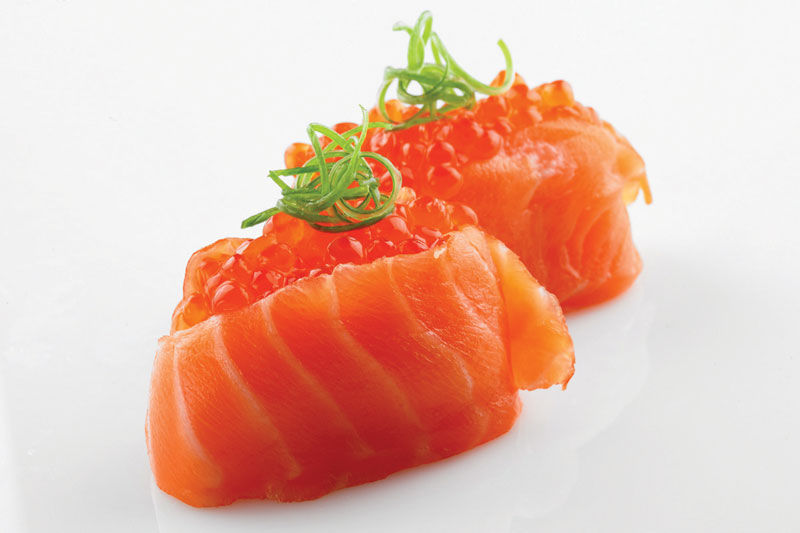
b.3. APPEARANCE | PRESENTATION - Photo [Color | Texture | Size] and Brief Descriptions
b.3.a. No sign of foreign element such as water crystal or moisture inside a food or processed food package
b.3.b. Color of the item as documented (high resolution photos) in the Guidelines - example for freshness (maybe very light pinkish for chicken whole leg skinless or skin on)
b.3.c. Texture of the item as shown in Photos - degree of smoothness and fibrousness for example
b.3.d. Size Range
b.3.e. Packaging - NO damage, leaks, dirt
b.3.f. Fatty Parts requirements within the Parameter (high resolution photos)
b.3.g. etc.
b.4. SHELF LIFE PARAMETERS (depends in the receiver: Division for example: Factory Plant, Distributors, Dealers, Retailers and End Consumers)
b.5. WEIGHING Scale - Graduation, Capacity
b.6. SMELL descriptions and Control Sample Reference
b.7. TEMPERATURE - Pyrometer for an example
b.8. TASTE Profile description and Control Sample Reference
b.9. TEXTURE description and Control Sample Reference
b.10. SOUND (if applicable) - crispiness, etc.
b.11. WORKING CONDITION for machine, and related - speed, temperature, others
b.12. Others
PROCESSES FOR COMPLIANCE:
Suppliers' Delivery Receiving preferably once a week during day at lean time period to optimize man hour, equipments and facilities
1. CONDUCTS PPS-QIP
Percentage Per Product SKU or Complete
1.a. Facility
1.b. Assigned QC who will perform
1.c. Assigned Warehouse Receiver
1.d. QA for Spot Compliance Audit
1.e. Operations Auditor may do Spot Audit
1.f. Warehouse In-Charge for Spot Compliance Audit
2. WAREHOUSE RAW MATERIALS & SUPPLIES "Receiving and In Queue"
2.a. Facilities
2.b. Involved Organization
Warehouse Receiver
Warehouse In-Charge for Spot Compliance Audit
Handlers
QC
QA for Spot Compliance Audit
Operations Auditor may do Spot Audit
2.c. Control Forms with Serial #, # of copies with cut-off time signatories, attachments, Tally Sheet, IT and others
2.d. Piling per SKU if bulk per Pallet with Tag (Item name or code, packaging, UOM & Weight | Quantity, Shelf Life Date, Received by and time, QC approved and time, and so on)
2.e. Piling of Assorted SKUs (heavy and bulky at the bottom, to lightest and smallest) per Pallet
with Tag
2.f. Proper Turn-Over
2.g. Others
3. Handling [Forklifts c/o Engineering Department - battery operated for Foods, Push Carts, etc]
3.a. Forms, People Involved for Accountability
3.b. Equipments - Clear, Sanitized, Hygienic, Well Maintained
3.c. Others
4. WAREHOUSE RAW MATERIALS & Supplies INVENTORY Management and Operations
WAREHOUSE FROZEN GOODS TEMPERATURES PARAMETERS
WAREHOUSE CHILLED GOODS TEMPERATURES PARAMETERS
WAREHOUSE DRY GOODS TEMPERATURES PARAMETERS (normally ambient - ceiling insulation)
(a) FIFO Rotation and Replenishment Standard Procedures with Cut-Off Time
a.1. FIFO Rotation and Replenishment Lay-Outs (Floor, Racking, Shelves)
a.2. Racking (Shelves Levels | Bins - Bottom for Oldest while New on topmost)
a.2.1) each Column Levels assigned to one Product SKU (note: not all SKUs to have Levels for it. Only those with Volumes or depending on the Lead Time of the Suppliers)
a.2.2) fast moving SKUs nearest Issuance Area
a.3. Others
(b) Packs Per SKU (Common)
b.1. Pack A - May be in Master Carton or Plastic Bag
b.2. Pack B - Loose Pack A (Pack B pieces)
b.3. Pack C - Loose Pack B (Pack C pieces)
Others have more packs like the Cigarettes.
(c) Shift Proper Turn-Over - Tally Sheets with Supporting Documents
c.1. Tally Sheet Per Category (Stocking) - SKUs are sequenced based on the Physical Racking | Shelving Systems for smooth flow (no Criss Cross) and economical time & motion.
FOR PHARMACEUTICALS [SKUs per Gondola BIN Shelves - Direct Display Selling]
Each SKU, for example in tables:
1. Sealed Mother Boxes are positioned at the innermost or last in a Bin Column
2. Open Box 2 for the Sheets
3. Open Box 3 for the loose pieces
In TALLY SHEET SKUs Sequence (No Criss Cross When Tallying for Proper Turn-Over):
Biogesic has 3 Packs. Each SKU has 3 columns: Pack A, Pack B, Pack 3
Authorized Staff can only ...
1. Open Sealed Mother Box when Loose Sheets remaining is good for a day's demand
2. Cut Sheet to Loose Pieces when remaining is good for a day's demand
FOR CONVENIENCE STORE at the Direct Selling Area Gondola Shelf BIN
Each SKU, for example OISHI Prawn Crackers | Regular Flavor at 40 grms per Pack C
1. Say, this SKU occupies (reserved | allocated) 5 BINS Columns
Each Column Bin to have 10 rows pack C
2. Followed by Rinbee Cheese Sticks at 40 grams per Pack C. Same as Oishi allocations.
In TALLY SHEET SKUs Sequence: Oishi Reg. 40 grms for 1st item, followed by Rinbee (No Criss Cross)
(d) Sanitation, Hygiene, Temperature, Humidity preferably every early morning (preparatory)
(e) CUT-OFF TIME receiving of PRODUCTION'S REQUIREMENTS Per Day for WAREHOUSE PREPARATIONS (Staffs Optimization over usage of time & motion | momentum of tasks).
(f) CUT-OFF TIME for Issuance to Production (Handling - Warehouse Helpers | Forklift Operator), QC Staff may conduct the PPS-QIP with the Production Assembler (authorized to receive) in the presence of the Warehouse Helper. Transmittal Form to be filled-up and signed by the involved staffs.
(g) Others
5. PRODUCTION per Assembly (Pre-Requisites to Stages)
Refer #4 letter "e" above
(a) Production Plan base on SCM Finish Goods SKUs' EOQ
a.1. Request Procedures with Cut-Off Time (# of copies, signatories, attachments) to Warehouse Raw Materials and Supplies
a.2. Etc.
(b) PPS and QIP Processes upon Receiving from Warehouse
b.1. Form or Log Book
b.2. Etc.
(c) PRE-OPERATIONS (Lot)
c.1. Settings Procedures base on PARAMETERS for control of Performance Metrics
c1.1. FOR CHOPPING | SLICING
[1] Parameters such as
[1.1] U-Formation Assembly Lay-Out of All the Materials are complete and clean. Process Flow from left to right.
[1.2] Left hand side - all meats, vegetables, etc.
[1.3] Center (in front) of the Assembler - Chopper | Slicer - Production
[1.4] Right hand side - a Tray where he | she place all the batch cut meat (per menu)
[1.5] Height of Working Table for Right Working Posture where his | her elbow within 45 to 90 degree angle parameter (comfortable chopping | slicing movement) or with Stool since Operator shall not be going anywhere just to chop | slice for economical processing (momentum)
c.1.2. FOR COOKING PREPARATIONS
[1] Settings of Parameters such as
[1.1] Temperature of Thawed Meat, and Oil on pan per batch. Note: In Parameter Measurements.
[1.2] Number of Minutes or Timer to reach desired
[1.3] Ingredients with the use of Weighing Scale preferably Digital (Graduation, Capacity), Measuring Cups, Spoons
[1.4] Utensils - every use to clean (see contamination)
[1.5] Everything has to be complete per Assembly or Stage such as
[1.5.a] Ingredients, utensils, etc. - No multiple handling and to prevent next assembly personnel from waiting
[1.6] Everything are in proper places (U-Formation of Assembly Process Line - Sequence of Stages) for example from left to right
[1.6.a] Left - all ingredients
[1.6.b] Right - all WIP finish goods Batch ready for next Assembler to use.
[1.7] Others
c.1.3. MANUFACTURING Machines (non-food)
[1] Settings of Parameters
[1.1] Temperature
[1.2] Speed
[1.3] Heating
[1.4] Actual Production
[1.5] Others
c.2. Etc.
(d) ACTUAL PRODUCTION (Batches)
See to it that All ingredients, utensils and others are complete and in proper position (U formation for smooth operation)
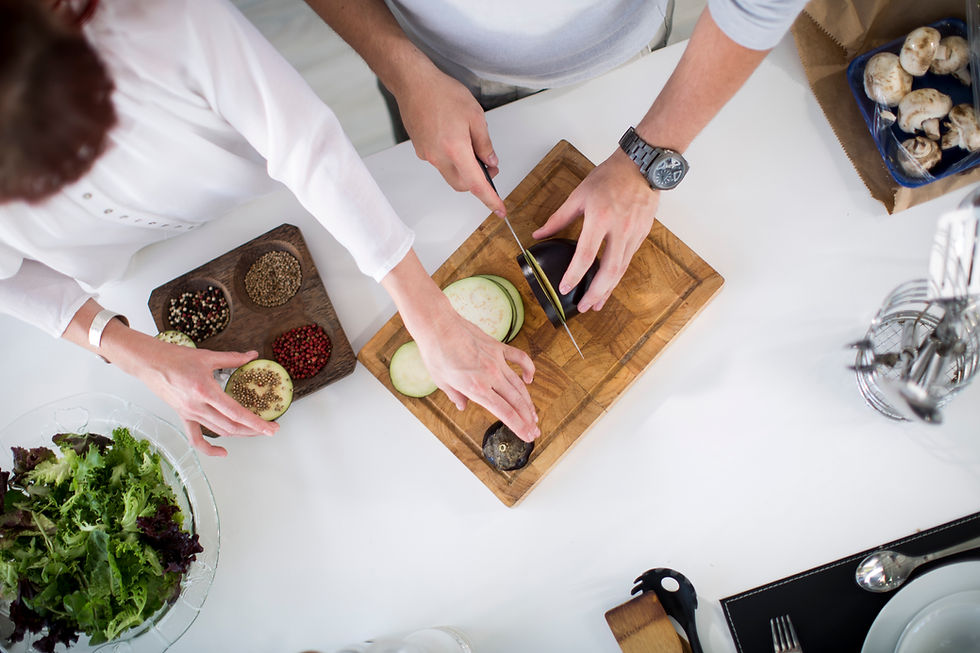
(d.1) FOR CHOPPING | SLICING
U-Formation Process Flow Working Table Lay-Out
Height of the Working Table
Economical and Safe Distance to Next Operator
[1] Parameters per meat menu example pork. However, parameter of weight volume good for Number of Servings in Commissary Batch
[1.1] Thickness, length and width
[1.2] Cut against fibers
[1.3] Others

(d.2) COMMISSARY Big Batch Production Processing | Cooking Section
U-Formation Process Flow Working Table Lay-Out
Height of the Working Table
Economical and Safe Distance to Next Operator
[1.1.] When Thawed Meat and Oil on pan reached Cooking Parameter Temperatures, Starts Cooking
[1.2] Monitor Number of Minutes for each side of the meat to be turned over
[1.3] And so on ... cooling, packaging, etc.

(d.3) FOR RESTAURANT Customer Orders,
U-Formation Process Flow Working Table Lay-Out
[1] Ingredients on the Left
[2} front of the Operator to Production
[2a] each ingredients in measuring cups or spoons
[3] right hand side for yields per menu tray
Height of the Working Table
Economical and Safe Distance to Next Operator
[1.1.] When Thawed Meat and Oil on pan reached Cooking Parameter Temperatures, Starts Cooking includes the Seasonings and other ingredients
[1.2] Monitor Number of Minutes for each side of the meat to be turned over
[1.3] Cooked food on plate (intended for that menu)
[1.4] Next Assembler for Presentation Standard
[1.5] Handler to QC Dispatch
[1.6] QC has to ensure the dishes have passed all parameters before dispatching to Waiters (usually right a bell)
(d.4) Others
(e) POST OPERATIONS (Lot)
(f) Partial Transfer (WIP to Next Assembler Stage or FG to Warehouse FG) - Standard Bulk Handling
Subject to QC Dispatch
6. WAREHOUSE FINISH GOODS
(a) PPS and QIP to be conducted by QC Staff with the WFG OIC
a.1. Van Temperature
a.2. Products for turn-over
a.3. Etc.
(b) Receiving
(c) FIFO Rotation and Replenishment
(d) CUT - OFF TIME Receiving of Delivery Requirements per Van's Drop Sequences (A day before)
(e) Preparations for Issuances (for Finish Goods) - base on Vans' Loading Schedules intended for deliver
e.1. Drop System Lay-Out
e.2. Each Outlet Customer Piling Standard
e.3. Etc.
(f) Issuance - Proper Cross Functional Turn-Over
QC Staff to conduct PPS-QIP in front of the Driver | Helper with the presence of the WFG OIC or Staff
7. LOGISTICS
(a) Vans' Master Route per Day for Drop System Schedules
(b) Other essential procedurals
7.1. Deliveries to ...
By Area (Regional, etc.)
(a) Distributors (Regional)
(b) Dealers (Regional Areas)
(c) Retailers (Regional Areas)
8. OUTLETS
Outlet Manager | QC Staff to
(a) ensure Van's Doors are sealed and then, check the Temperature
(b) conduct PPS-QIP in front of the Driver | Helper
ELECTRONIC REPORTS (Auto Email, Text, Viber, OneNote, etc. for MBO Decision Making)
REAL TIME & ACCURATE AUTO - GENERATED MIS particularly the PERFORMANCE METRICS on PRODUCTS QUALITY with ANALYSIS in relation to APPROVED PPS PARAMETERS from Raw Data Entry Transactions including Tally Sheets (may use Tablets)
1. QC Manager - 3Cs with QA Manager
2. QA Manager - 3Cs with Plant Sr. Manager and QA Manager
3. Raw Materials and Supplies Warehouse Head - 3Cs with Purchasing & Production Department Heads, as well as the Plant Sr. Manager
4. Purchasing Manager - 3Cs (communicate, coordinate & cooperate) with Suppliers and Warehouse Raw Materials and Supplies Head
5. Production Manager - Production Scheduling and 3Cs with Warehouse FG and Raw Materials Heads, Plant Sr. Manager
6. Warehouse FG Head - 3Cs with Sales Manager | Operations Manager | SCM | Logistics Head, Production Manager and Plant Sr. Manager
7. Plant Sr. Manager - 3Cs with SCM | GM | Sales Manager | Operations Manager, All his | her Immediate Subordinates
8. Sales Manager - 3Cs with Operations Manager and WFG | Logistics Heads, Plant Sr. Manager
9. Operations Manager (National to Regional then to Area Heads) - 3Cs with Branch OICs, Sales Manager, Plant Sr. Manager, WFG Head, Logistics
10. Logistics Head - 3Cs with WFG and SM | OM (National) | Branches Heads, Plant Sr. Manager
11. Operations Audit Head - Comprehensive Variance Analysis for Inventory Control from Raw Materials to WIP then to FG and Others
12. Compliance Audit Head - Comprehensive Analysis to improve Compliance
13. Finance for Cost - Profit and Adjustments in Budget Schedules if necessary, etc.
14. Administration for Compliance and Incidents Accountability Management throughout the entire Organization
15. HRD for Training Programs, etc.
ORGANIZATIONAL CAPACITY | Learning and Growth
TQM (as an Approach to Management that Embeds Awareness of Quality in All Organizational Processes. Improving process efficiency brings about many benefits in terms of Costs & Time)
*Process Roll - Out Plan IMPLEMENTATION Guidelines including Hands-On Training
PRODUCTS QUALITY CONSISTENCY PROGRAM
HANDS-ON ON THE JOB TRAINING PROGRAM (Limited Only to those mentioned above in the 3 Perspectives of BSC KPI-SMART)
1. OBJECTIVE | Purpose - Critical Success Factors | KRAs of the Training Program
1.a. That all involved Internal Resources (Command Accountability Chain and Cross Functional management up to cascaded Micro Units Personnel) will be knowledgeable, and skilled to do their part in the Right Way at the Right Time in the Right Place. Includes close Communication, Coordination and Cooperation. Moreover to the Management, the Organizing, Orchestrating and Overseeing to ensure or at least minimize the impact to the Company and costs.
The involved organization shall have to see to it that ALL Inventories have PASSED and within the PARAMETERS including the Shelf - Life
2. PRODUCTS QUALITY CONSISTENCY | PPS-QIP TRAINING Program
An In-Depth Step By Step Organizational Processes concerning All Involved from both Internal and External Suppliers and Customers
Being able to strictly implement and apply the PPS-QIP Protocols consistently.
The Author is taking this opportunity to train the READER in his best here and here it goes.
Here's SOME QUESTIONS & GUIDELINES IN ORDER TO DEVELOP THE TRAINING PROGRAM limited to the INTERNAL BUSINESS PROCESSES indicated above, The Training METHODS, and THE Training FRAMEWORKS
2.a. What do the involved PPS-QIP Organization need to know?
(a) That there is an Organizational Processes Standards in order to have QUALITY CONSISTENCIES in inventories to prevent spoilage and cost of money.
(b) How is the Mechanics? And How To ORGANIZE the TEAM?
b.1. Command Accountability Chain and Cross Functional Management up to cascaded Micro Units Personnel Structure
b.2. Each Ones KRAs, Key Functions, and KPI-SMART Parameters and Metrics
b.3. Procedures including the Excel Tools and How it works
(c) Determine or Ascertain to ensure they fully understand?
(d) ORCHESTRATE each one base on their Key Functions, the KRAs, and the KPI-SMART Parameters and Metrics
(e) OVERSEE by closely guiding, mentoring, and coaching in the SIMULATION.
(f) Evaluates and Analyzes with the concern from time to time where to improve. Plan the courses of Actions. Use BSC KPI-SMART Framework. For Sample, Click https://stangsanto.wixsite.com/kpi-smart/frameworks
2.b. What Protocol to ensure compliance?
(a) If you are the General Manager, what Metrics do you need to see and at what time? From whom? What if did not do? What corrective actions to take?
(b) If you are the SCM, what Metrics do you need to see and at what time? From Whom? What if did not do? What corrective actions to take?
(c) If you are the QA Officer, what Metrics do you need to see and so on?
(d) If you are the Factory Plant Sr. Manager, what Metrics do you need to see and so on ...
(e) If you are the Department Manager receiving, stored, issuing, what Metrics do you need to see ...
(f) Have Periodical Reports from the OPERATIONS | COMPLIANCE Auditors.
3. What MATERIALS are needed in the Training including the Simulation? Budget?
4. What Facilities are needed in the Training including the Simulation? Budget?
5. Set Up the Training Schedules for the Management and the Trainees
6. Preparations
7. Post Evaluation for improvements
A. TRAINING for the TRAINERS
1. Objectives | Purposes
1.a. To equip, develop and enhance the Leadership of the Trainers (the Command Accountability Chain and Cross Functional Management)
1.b. Preparing the Officers in closely preparing their subordinate team in the Simulation
1.c. Others
2. PPS-QIP Trainers' Program Covers
2.a. How will a QA Manager trains the QC and Other Managers for the latter to succeed in complying to his | her role? Moreover, how will he | she to build up its immediate subordinates to be successful? QC Manager's key | direct reports are:
(a) QC Supervisors (immediate subordinates are the QC Section Heads while the latter's, the QC Staffs)
2.b. How the Operations or Stores Chain Officer trains his | her immediate subordinates (If National to Regional)? Plus, how will this Regional or Area Head equip its direct reports (Outlets Heads)?
2.c. How the Plant Executive will build up his | her direct reports such as the Warehouses Manager, Logistics Officer, Production Manager?
3. Who are involved?
(a) Balance Command Accountability Chain and Cross Functional Officers up to cascading to their respective Micro-Unit Personnel
a.1. General Manager
a.2. SCM
a.3. Sales Manager (has to be knowledgeable)
a.4. Operations Managers (National | Regional | Areas), Retail Outlets' Heads and Staffs
a.5. Marketing Manager (has to be knowledgeable)
a.6. Sr. Plant Manager
a.7. Logistics In-Charge
a.8. Warehouse Finish Goods In-Charge
a.9. Production Manager
a.10. Warehouse Raw Materials and Supplies In-Charge
a.11. Purchasing Manager (has to be knowledgeable)
a.12. External Suppliers (in fact, they have to train and update the QA Officer)
a.13. QA and QC Staffs to ensure Quality Products
(b) What are each ones KEY RESULTS AREA? KEY FUNCTIONS? KPI-SMART PARAMETERS AND METRICS with Cut-Off Time? Comprehensive Job Description Contract
(c) The CORE Management Frameworks
4. The In-depth Method (Step By Step) to address the following ...
(a) What each one has to ensure ahead of time base on the need of its External and Internal Customers? When? Where? How?
5. How to ensure compliance?
6. Materials Needed prior to Simulation | Implementation
6.a. Process Flow Charts
6.b. Forms (# of Copies), Specimen Signatories with Cut-Off Time
6.c. Attachments required in sequence
6.d. SoftWare for Encoding
6.e. Concerned Officer's MIS (linked from raw data entry if Excel)
6.f. Economical Lay-Outs for Setting Up
6.g. etc.
7. Facilities Needed
7.a. Training | Conference Room
(a) PC or Laptop
(b) Video to document and for eManual to be used for future refresher course training
(c) etc.
7.b. Actual Site/s Simulation (refer number 2 above)
8. Others such as evaluation analysis ...
B. TRAINEES (Micro Units)
Trainers are Coached | Mentored in equipping, developing, enhancing the Trainees (Micro Unit Personnel). Their immediate subordinates.
b.1. What are their KRAS? KEY FUNCTIONS? KPI-SMART PARAMETERS AND METRICS?
b.2. Simulation
b.3. Post evaluation analysis for improvements
Comments